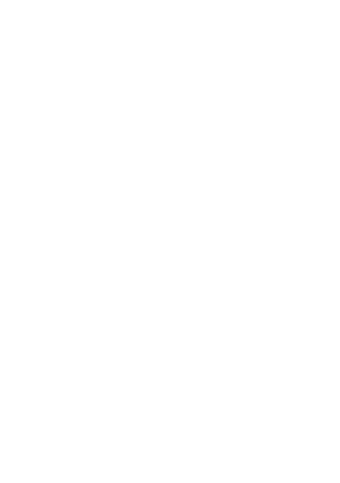
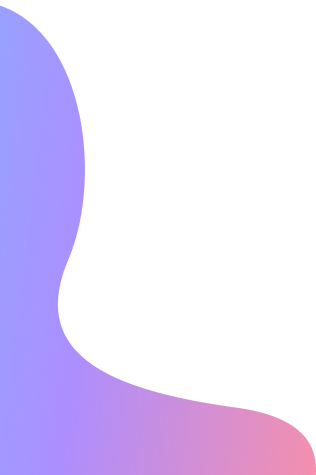
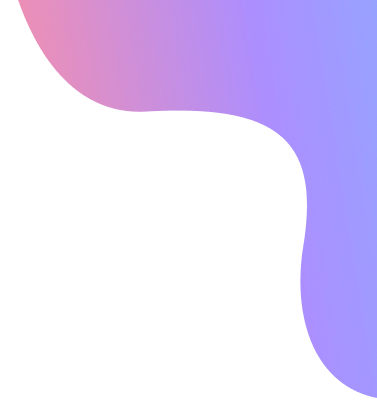
311 minutes (65% of every work day)
spent on non-productive activities.
A time study conducted by consultant Joel Levitt confirmed yet again how small a percentage of an hourly maintenance worker’s time is spent on “direct actual work.” In a 480-minute work day, Levitt’s research found that a typical technician spends:
24 minutes
receiving instructions
57 minutes
getting tools/materials
72 minutes
traveling to/from tasks
38 minutes
coordination delays
24 minutes
idle at the job site
24 minutes
late starts/early quits
48 minutes
authorized breaks/relief
24 minutes
excess personal time
Understanding
Maintenance Triage
- Triage is a management protocol that structures the incoming workflow by priority so that the most critical work is attended to first.
- The practice is most often used in hospitals and other healthcare settings, becoming particularly important in response to disasters, battlefields or other emergencies.
- Triage also has applications in non-healthcare businesses by creating a structure for prioritizing projects, updates, publications, and other timely corporate needs.
Inefficient and unsafe maintenance
In maintenance, breakdowns are usually responded based on :-
First come, first serve.
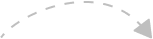
Highest number of complaints.
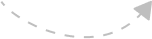
Complainant's rank.
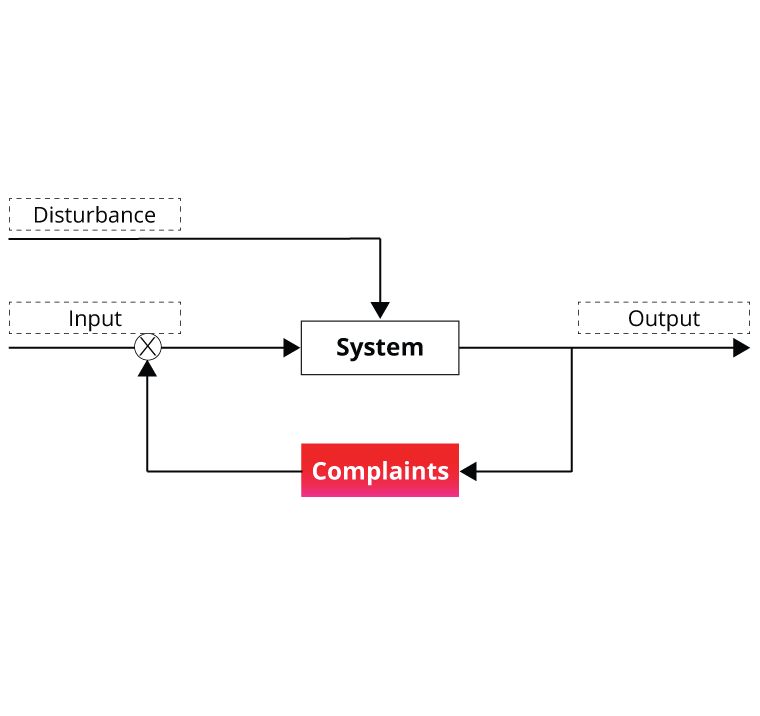
The Eisenhower
Decision Matrix
Maintenance triage safely responds based on the importance and urgency of equipment using Eisenhower Decision Matrix. The Eisenhower Matrix is a task management tool that helps you distinguish between urgent & important tasks so you can establish an efficient workflow.
Where importance is determined by : - equipment management number ≥ 12 and urgency is determined by history ≥ 0